The body man attached this area of panels with brazing and sheet metal screws, with welding elsewhere. Then the seams were covered with lots of lead. I would never have messed with this area, but here is where the lead was bubbling. After removing lead from the seams I found pockets where something didn't get along with the lead and steel living together. I wonder if it was a sort of oxidation, impurities in the lead, or the steel base not being totally prepared.
Wednesday, December 29, 2010
More Olds!
I am back at the '62 Oldsmobile, this time finishing the last rust areas and a leaded area that started bubbling. The passenger rear corner had bulges in the lead applied to cover the overlap seams where the rear corner piece meets the 1/4 panel. The factory did this the same way after spot welding the panels together. This particular area was redone when a new entire 1/4 panel was attached sometime early in the car's life. The liberal use of lead indicates this to me.
The body man attached this area of panels with brazing and sheet metal screws, with welding elsewhere. Then the seams were covered with lots of lead. I would never have messed with this area, but here is where the lead was bubbling. After removing lead from the seams I found pockets where something didn't get along with the lead and steel living together. I wonder if it was a sort of oxidation, impurities in the lead, or the steel base not being totally prepared.
So I began to remove all of the lead with careful heating, pushing soft blobs away and wiping the wet lead with a rag. The lead used seemed extensive; I also didn't want to put lead back onto a not-so-perfect seam full of crevices and overlap, being afraid that no matter how clean I get it, there would likely be remaining impurity issues. I didn't want the bulges to reappear after I finish this car. So I decided to remove the overlap areas entirely, and weld new sheet metal patches level with the outer area.
Forming little pieces was not difficult, as I had a nice pattern to follow. The curves were very easy since the patches were so small, only requiring using my hand and pliers to shape them. The main reason I made one small patch (and attached it) at a time was to keep the overall shape of this panel in line. This helped me avoid moving the middle panel out of alignment with the shape it needed to follow.
This is the only time I needed any other tool than my hand held pliers. I just needed a little bend on the brake.
Second to last piece being fitted for trimming.
Careful grinding, filing and a little picking with the body hammer left the pieces pretty smooth. Now I can use a little bit of filler and the area can be fully cleaned/scuffed for adhesion. No lead needed, either.
Not too bad!
Here's an area under the pass. door where I needed to make a new patch. The brake, stretcher and hammer-on-anvil were used for this little patch. Welds still look nasty, just waiting to be carefully ground smooth.
The body man attached this area of panels with brazing and sheet metal screws, with welding elsewhere. Then the seams were covered with lots of lead. I would never have messed with this area, but here is where the lead was bubbling. After removing lead from the seams I found pockets where something didn't get along with the lead and steel living together. I wonder if it was a sort of oxidation, impurities in the lead, or the steel base not being totally prepared.
Wednesday, December 22, 2010
XMAS OPENING TIMES !
XMAS 2010 : Our parts shop will close at 5.00 pm on Thursday 23rd December. We are open between Xmas & New Year on Wednesday 29th & Thursday 30th 10.00am -2.00pm. Parcel Force & Royal Mail will be collecting / delivering on these dates too !
We reopen as normal on Tuesday 4th January 2011 9.00 am. Website ordering and... e-mail quotes available throughout the holiday period. All orders placed before 1st January will be processed at the cheaper vat rate .
Sincere Xmas wishes to all our classic car fans around the world - I hope you have a safe , healthy and prosperous 2011.
Cheers
Andy
Sunday, December 19, 2010
Woodward Fab Bead Roller Modification
I've been wanting to try a bead roller. Ever since I began setting up the construction of my '30 Model A coupe I have wanted to be able to form floor panels and body patches that would use beads, grooves and flanges. Problem is, I don't want to spend $1,000 or more for a decent roller and set of dies. But through online searching I've found actually good information on the cheapo bead rollers from Harbor Freight and others. There is just one catch...they need major stiffening side to side and up and down.
The picture below is the one I decided to go with. It is from Woodward Fab, and comes with 6 sets of dies. It is made of solid steel plate, just shy of 1/2" thick, and has an 18" throat. It feels better than the Harbor Freight one, being a thicker plate (HF one is 3/8") and having grease fittings. It is also identical to the Eastwood economy model, likely from the same Chinese factory. Plus, the Woodward Fab tools in general have a good reputation, especially compared to HF.
The above picture isn't my attempt at advertising- I was just too lazy to remove the "super low price" artwork.
So I pulled my Woodward Fab bead roller out of the box, installed it on the vise, assembled it and gave it a try. The dies do their job, and it stays fairly lined up, but the frame plate has tons of flex! And most noticeable was side to side flexing. Now the plans to reinforce (and make it look pretty) begin...
The picture above shows one of the patterns I made for cutting the bottom plate. The green line is where the purchased frame plate would meet the added curved reinforcing plate that this pattern produces. I formed this and a top pattern (after lots of sketching) on Masonite with my little jigsaw, and then aligned the patterns to some 1/2" plate and plasma-cut the pieces.
Here is a picture showing the top plate and bottom plate welded to the Woodward Fab frame. I tried to give it an industrial look, like a tool in a vocational shop that has form-following-function (or maybe the other way around...) with an earlier appearance. You can see the welds are ground down and the paint from the original piece is ground off.
After using scrap from my generous boss Matt (Owner of the company I work for) and a '28 Ford torque tube, I came up with this neat stand assembly. It has an almost antique industrial look, but also spartan. It is still going to be top heavy, so I will bolt it to the floor.
Above shows another view, this of the backside. The 2"x2" square tube is actually the major reinforcement; it does more work than the vertical pieces I meshed with the original plate. This idea was copied from the very cool ideas I found online. The vertical round tube is scrap pieces I cut and lined up for holders of the dies not being used. I like the curvy-shaped plate I added to the pedestal tubing. It calms my fears of weak spots, and looks good too!
Here it is bolted to the floor. I used those female thread anchors that stay level in the concrete, so I can easily remove the bolts and move the assembly out of the way. The paint is the last drops of DuPont Variprime leftovers I had, given to me for free by an old neighbor. It is a 2-part etching primer, and I didn't want to see it go to waste. Plus, now I have something paint can bite to.

These two pictures show the assembled bead roller and the extra dies sitting on their holders.


This above pictures shows the first experiments with scraps from Creer Sheet Metal. This bead roller is going to be wonderful for floor pans, body reinforcements, and even patch panels. I see lots of possibilities!
This last pic shows the completed project including the wheel I made to operate it with. The crank it came with is not nearly as usable. I made this wheel from the foot rest of a broken bar stool, and the spokes/mounting assembly from channel scrap I scrounged from a spiral staircase I helped remove. It works with no noticed flex and cost was very low, unless you count my time and tools. But I wanted to build it...!
The picture below is the one I decided to go with. It is from Woodward Fab, and comes with 6 sets of dies. It is made of solid steel plate, just shy of 1/2" thick, and has an 18" throat. It feels better than the Harbor Freight one, being a thicker plate (HF one is 3/8") and having grease fittings. It is also identical to the Eastwood economy model, likely from the same Chinese factory. Plus, the Woodward Fab tools in general have a good reputation, especially compared to HF.

So I pulled my Woodward Fab bead roller out of the box, installed it on the vise, assembled it and gave it a try. The dies do their job, and it stays fairly lined up, but the frame plate has tons of flex! And most noticeable was side to side flexing. Now the plans to reinforce (and make it look pretty) begin...
These two pictures show the assembled bead roller and the extra dies sitting on their holders.
This above pictures shows the first experiments with scraps from Creer Sheet Metal. This bead roller is going to be wonderful for floor pans, body reinforcements, and even patch panels. I see lots of possibilities!
Friday, December 17, 2010
You can be sure of Shell
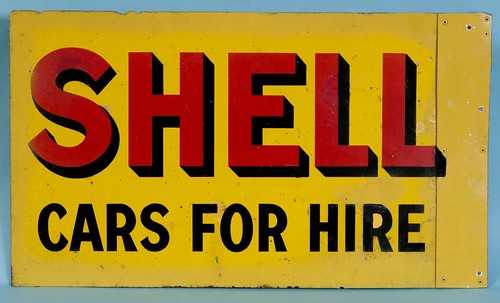

To kick start the New Year, Charterhouse will be selling a large Shell collection in their Classic Car, Motorcycle and Automobilia auction on Sunday 13th February at The Footman James Restoration Show.
Consigned from a Somerset fuel suppliers, the collection has been amassed over the last 50 years and includes many enamel signs, petrol pump globes, prints, advertising and related items estimated to sell for several thousands of pounds.
“It is a comprehensive collection, the likes of which rarely come to the market.” Commented Matthew Whitney. “It’s quite amazing to think that they have been in only one family ownership for the past several decades and will now go to only their second owner.”
Also entered in this sale is a 1973 Ford Escort Mexico Historic Group 2 rally car from a Cornish client. This has been fully rebuilt from a bare shell with receipts of over £60,000 and if offered for auction at a fraction of the re-build cost. This will be a turn key solution for any budding competitor in historic rallying and would enable them to compete immediately without having to go through the expense of having to source and rebuild a similar car.
For further information regarding this auction, or for advice on how to enter a vehicle or automobilia, please contact Matthew Whitney, Head of Department, at Charterhouse, The Long Street Salerooms, Sherborne, Dorset DT9 3BS, 01935 812277
or via email mw@charterhouse-auctions.co.uk
Captions:
A Shell Cars For Hire enamel sign
A Ford Escort Mexico Historic Group 2 Rally Car £25,000-28,000
Quick Links
Forthcoming Sale Previous Sale Sale Preview | Tel: (01935) 812277 |
Subscribe to:
Posts (Atom)